17 minutes seulement sont nécessaires pour transformer la surface d'une bobine aluminium en un support sensible à la gravure du CTP, dans la seule usine française de plaques d'impression offset. Mais pendant ces 17 minutes, les bobines vont passer à travers de multiples ateliers à la pointe de la technologie.
Agfa nous a ouvert les portes de son usine de plaques offset située à Pont-à-Marcq (Pam) dans le Nord. Suivez-nous pour une visite guidée de ce site qui produit chaque semaine 500 000 plaques d'impression offset.
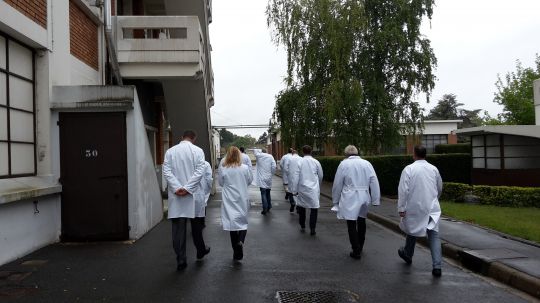
Chaque semaine 200 rouleaux d'aluminium livrés
Environ 200 rouleaux de 320 mètres de long de différentes laizes arrivent chaque semaine à Lille. Pam travaille avec l'usine Agfa située à Leeds en Angleterre.
Thierry Coutier, directeur du site Agfa de Pont-à-Marcq, nous explique le processus : "Le site de Leeds prépare les rouleaux bruts d'aluminium. L'aluminium est grainé et anodisé afin d'avoir les propriétés physiques nécessaires à l'emploi final sur les machines d'imprimerie."

L'accumulateur qui fait danser les bobines sur 3,5 mètres de haut
Tous les rouleaux sont montés sur de multiples bobines qui permettent d'étaler l'aluminium dans toute l'usine afin de recevoir l'émulsion sensible au laser du CTP puis de sécher.
La fin d'un rouleau aluminium est collée avec le bord du rouleau suivant. Ce collage par bande collante est un système unique qui a nécessité plusieurs mois de développements aux ingénieurs de l'usine française et qui a été déployé sur les autres sites du groupe.
Ensuite vient la zone de l'accumulateur. Comme sur une presse rotative, cette partie qui sert de tampon permet d'appliquer différentes tensions à la bobine et de tempérer sa vitesse.
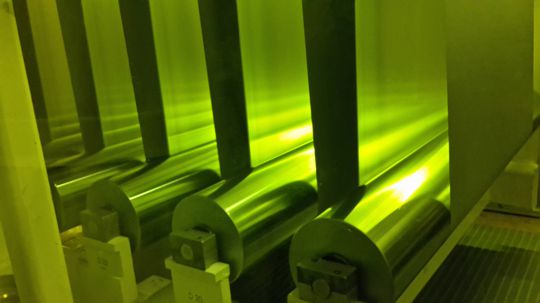
Dans cette pièce impressionnante toute en hauteur, les mandrins sur lesquels sont montées les bobines d'aluminium s'élèvent et descendent sur 3,5 mètres faisant varier la longueur de la bande.
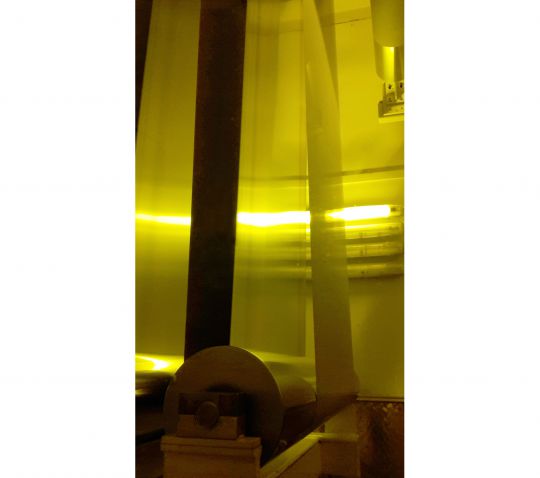
La tête de coulée, le cœur de l'usine
Après le déroulement juste après l'accumulateur se trouve le cœur de l'usine : la tête de coulée là où réside le secret de fabrication de la marque qui a fait sa réputation. Blouse, charlotte, sas de sécurité et photo interdite dans cette toute petite pièce où réside le secret de fabrication de la marque qui a fait sa réputation.
La machine qui dépose l'émulsion ressemble à un traceur très grand format, déposant l'émulsion sur l'aluminium qui défile à la verticale.
Cette machine est particulièrement performante par rapport aux autres salles de coulée du groupe, puisqu'elle produit 150 m/min de plaques contre environ 50 m/min pour les trois autres sites Agfa.
L'opérateur débute la semaine par les bobines les plus larges pour aller vers les plus étroites. Cela permet de ne pas tacher la machine avec l'émulsion.
Lors de la coulée, un système d'aspiration garantit une épaisseur uniforme de l'émulsion. Un litre d'émulsion permet de produire 30 m2 de plaques. Quatre émulsions sont appliquées pour réaliser les quatre plaques thermofuses d'Agfa.
Le raccord entre deux bobines d'aluminium est automatiquement détecté et la coulée est interrompue à cet endroit.
La préparation de l'émulsion, le rôle du solutionneur
La tête de coulée est directement reliée à de grandes cuves métalliques.
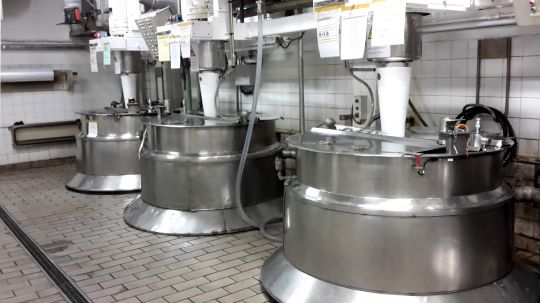
Dans ces cuves, le solutionneur prépare l'émulsion en mélangeant une trentaine de produits. Cette solution passe ensuite par un système de filtration qui alimente la machine de coulée.
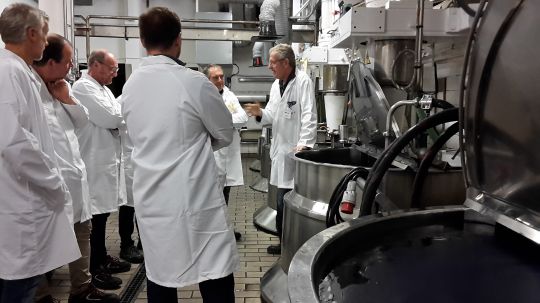
Un séchoir de 200 mètres de long
Cette émulsion fraîchement déposée sur l'aluminium doit sécher. Pour cela, 200 mètres de séchoir ont été répartis sur plusieurs niveaux sur les 80 m de long de l'usine. Cette zone comporte 14 sections différentes dans lesquelles la température varie de 40 à 70 degrés.
À la fin du séchoir, la position de la bande collante détectée lors de la coulée est déterminée grâce à sa position détection en tête de coulée : le raccord est alors coupé pour recréer, à la volée, une bobine sur un manchon vide.
De nombreux systèmes de contrôle qualité
Après le séchoir, un premier système avec 24 caméras permet de détecter les défauts. Puis un deuxième système par laser vérifie l'émulsion en contrôlant la brillance et enfin un troisième système inspecte du dos de la bobine.
"Car nous ne coupons pas les plaques directement, précise Thierry Coutier. Elles sont d'abord rembobinées et le dos ne doit pas abîmer le côté émulsion".
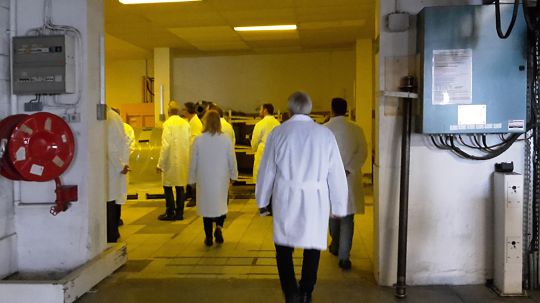
Les bobines transformées en plaques de différentes tailles
Puis, 17 minutes après la dépose de l'émulsion, les bobines sont prêtes à être découpées en plaques de différentes tailles.
"Pour cela, les rouleaux sont déroulés un par un et la bande est découpée au format demandé par le client et rangée par piles de plaques", nous décrit le directeur.
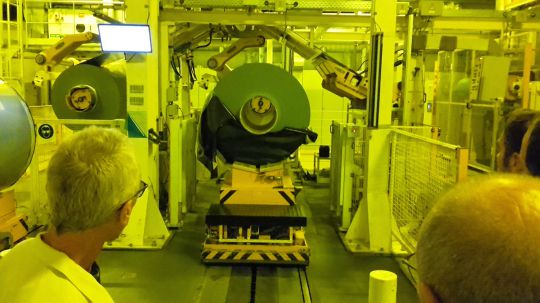
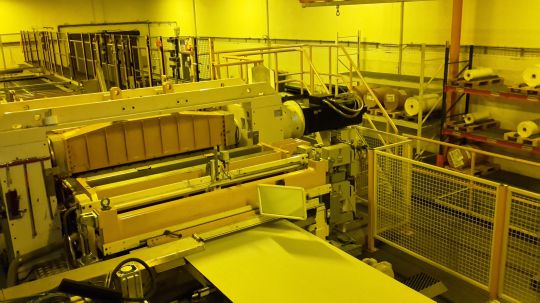
"Des petits inserts en papier permettent de compter les plaques et de créer des séparations physiques entre les différents paquets sur la pile."
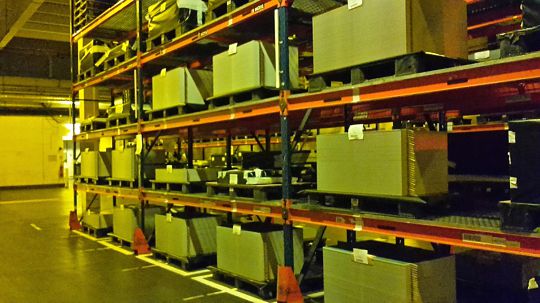
Il ajoute : "Un système d'inspection scrute en temps réel le défilement de la tôle et élimine automatiquement toutes les plaques sur lesquelles un défaut est détecté. Un contrôle supplémentaire est opéré par le conducteur de la ligne. D'autres prélèvements seront opérés par le service contrôle pour garantir le plus haut niveau de qualité".
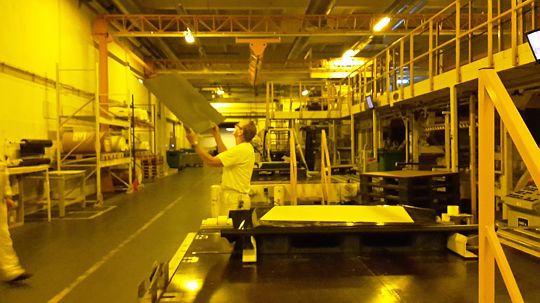
L'emballage, un atelier fortement automatisé
Les plaques sont ensuite acheminées par des robots à l'atelier emballage.
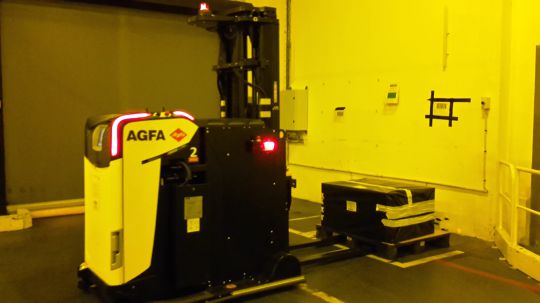
"Leur emballage varie en fonction des clients, leur localisation et besoin. Cette partie est fortement automatisée. Puis le service logistique distribue les produits, soit à travers le magasin central situé à Anvers ou directement à partir de l'usine comme pour le Japon, les États-Unis ou l'Espagne".
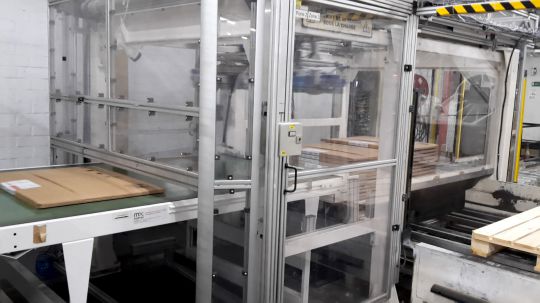
L'usine est également équipé d'un atelier de fabrication sur mesure des blanchets. C'est l'un des six ateliers français spécialisés dans ce revêtement caoutchouté et le seul dans l'Hexagone du groupe Agfa.